

:strip_icc()/pic6047332.jpg)
In well-sealed panels, however, the release of this blowing agent is slower. Both contain a blowing agent that escapes over time, reducing the R-value. Polyurethane and isocyanurate foam-core panels have a nominal R-value of around R-6 to R-7 per inch (25.4 mm) of thickness. This is a technically complex and chemically volatile process, but it produces a strong bond between the foam and the skins. Since it is difficult to achieve a strong bond between polyurethane or isocyanurate and wood, most manufacturers inject the foam between the two wood skins with specialized equipment. Wood composition sheathing may be glued to polyurethane and isocyanurate slabs of insulation in the same way as EPS panels. Polyurethane/Isocyanurate Foam-core Panels Manufacturers can make some panels as large as 81♂81 inches (1.06♇.14 m) these require a crane to erect. A common wall panel is 41´81 inches (1.04♁.06 meters ) and weighs 110 pounds (50 kilograms ). Wall panels made of EPS foam are typically 3 1/2 inches to 7 1/2 inches (89-190 mm) thick while Ceiling panels are 5 1/2 inches to 11 1/2 inches (140-292 mm) thick. Unlike the other types of foam insulations, beadboard is made using a pentane blowing agent. EPS foam-core panels have a nominal R-value of about four per inch (25.4 mm) and it remains relatively constant as time passes. EPS, commonly known as beadboard, adheres to the wood sheathing. The majority of foam-core panel manufacturers produce EPS panels. Manufacturers are currently examining ways of using cementitious or fibrous core insulating materials in place of these plastic insulations. Types of Foam-core Panelsįoam core panels use a rigid insulation core made of one of three plastics: expanded polystyrene (EPS), polyurethane, or polyisocyanurate, a polyurethane derivative. The airtightness of the foam-core house (measured at 0.21 air changes per hour ) was marginally better than the conventional wood-framed house (measured at 0.27 ach). The FSEC also monitored side-by-side foam-core and conventional wood-framed structures in Kentucky for about two winter months. This contradicts previous testing by the Florida Solar Energy Center (FSEC) that found a 12 to 17 percent energy savings from using foam-core panel construction. Scientists at the National Renewable Energy Laboratory (NREL) found that both types of construction performed as expected from their nominal R-values. In 1993, a structural insulated panel home was built adjacent to an identical, conventional wood-framed house. Openings in the panels, such as for doors and windows, may be precut at the factory or cut with standard tools by the builder at the construction site.
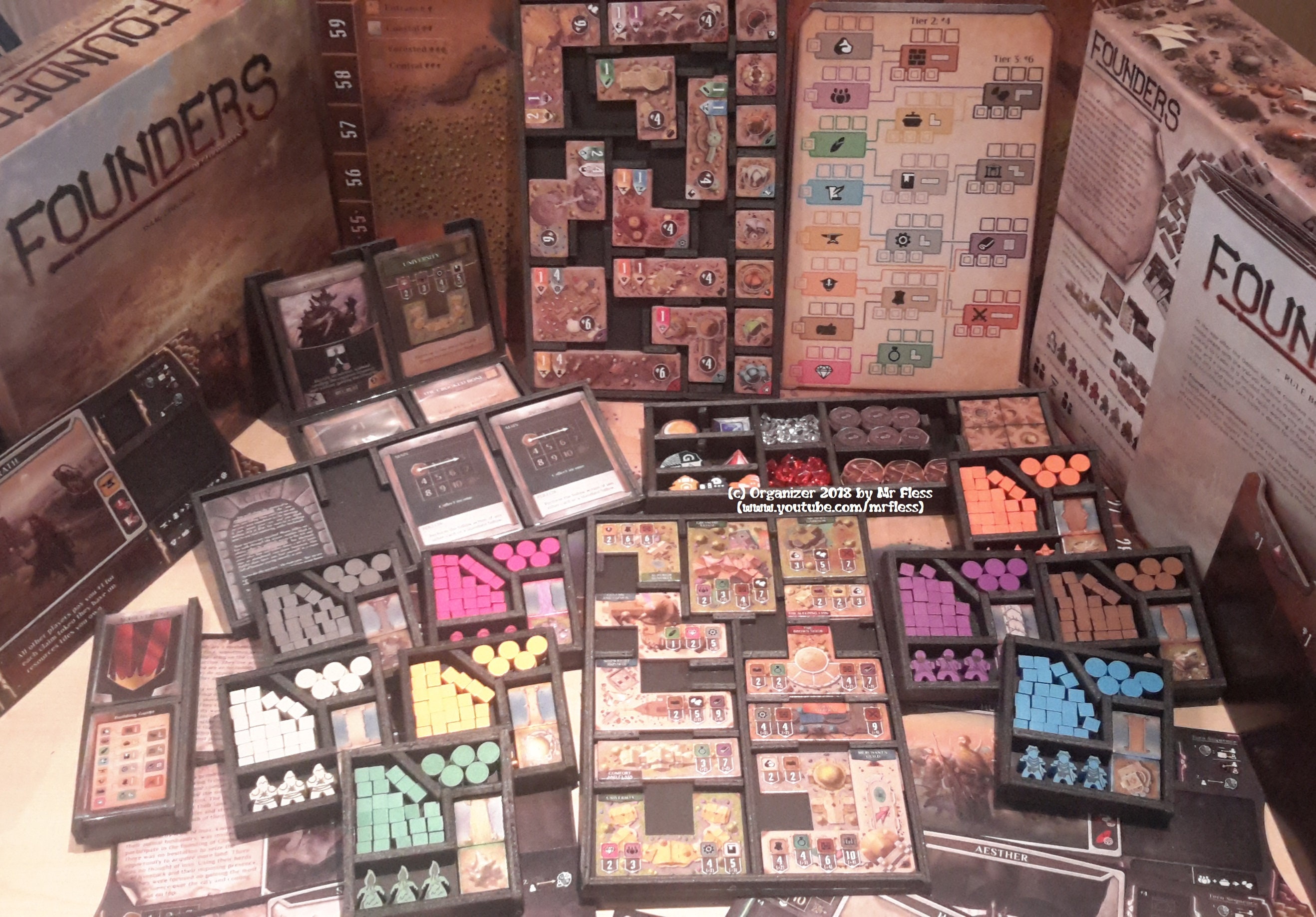
It takes as little as one to three days to fully erect and weatherproof the shell of a foam core, panelized house. The builder needs only to assemble the pieces on the site. Sometimes drywall is the only interior sheathing option for these wall panels.įoam core panels are a key component of "panelized housing," where specific fabrication occurs in a factory. These panels are strong: a wall with two, half-inch (12.7 millimeters ) thick OSB skins is nearly three times stronger than a conventional 2♄-inch (51♁02 mm) stud wall.Īlthough non-structural foam core panels are not designed to provide primary structural support, they may be used to enclose curtain wall structures like timber frames. When used in house construction, structural insulated panels may make up the primary structural support. The two basic types of foam-core panels are structural and non-structural.
